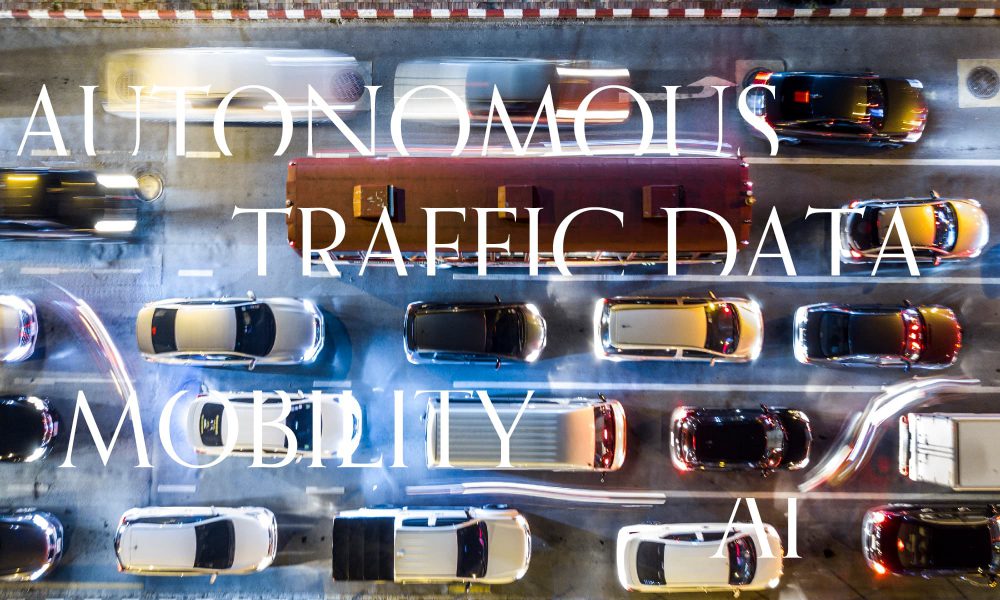
工場の IoT 化は社会の発展に重要な要素です。
本記事では工場や製造業が直面している課題を挙げ、IoT化による解決できる問題やメリット、実際の工場の IoT 化の例を詳しく紹介し、工場のIoT化による生産業界の変化を伝えます。
工場・製造業の課題
工場や製造業における課題は主に以下の4つがあります。
80%の情報が整理されていない
製造現場において、整理されていない情報は80%といわれています。
多くの情報が整理されていないことで、工場の運営に影響が出ます。
工場の作業スケジュール、商品に関する情報、従業員の数、職場環境、作業効率に関わる事実など、確認を怠ることでトラブルにつながりかねない要素は多くあります。
発注品の詳細を正確に把握できない
工場でよく起きる問題に発注ミスがあります。
発注された品の詳細を把握していないと、間違った作り方で大量の商品を完成させてしまったり、作る必要のある商品の数を見誤ったりなどのリスクが生じます。
発注ミスがあると工場側に損害が及ぶだけでなく、取引先との信用問題にもつながります。
一度のトラブルだけで計画に悪影響が出る
工場での作業は定められたスケジュールに従って行われます。
しかし機械故障、部品切れ、工場の生産能力を超えた商品を受注してしまうなど、トラブルのパターンも多岐にわたります。トラブルが起きるたびにラインを停めなければならないケースもあり、納期に遅れてしまうこともあります。
納期の遅れも工場側の損害や取引先との信用問題に至りかねません。
人手不足
現代社会では人手不足が問題になっており、製造業も例外ではありません。
少子化が背景になっているうえ、肉体労働を嫌う若者も多く、人が集まらない工場も少なくありません。人手が足らないことで、生産能力を向上できないと悩む工場も多いです。
作業者の事故
工場では作業者が巻き込まれる事故が起きるケースもあります。
作業者の事故で労働災害が認定されれば、工場は一気に信頼を失ってしまいます。労働災害が起きるケースには、作業者が安全でない状態で作業を強いられていた場合もあります。
以上のような事態を防ぐ目的でも、IoT導入にする作業環境の改善は不可欠です。
工場×IoTで解決できること
工場などの製造現場をIoT化することで、5つの問題解決が見込まれます。
多くの情報を「見える化」できる
IoT導入により、それまでなんとなくでしか把握できなかった情報を可視化できます。
IoTには様々な観点から対象のデータを数字などで「見える化」できるため、情報を正確に把握できないことで発生するトラブルを未然に防げます。
生産性や品質が向上する
IoTでデータ化された情報をもとに工場をコントロールすることで生産効率を上昇させられます。製造品に関してもデータから受けたヒントをもとに、従来より短時間で完了する製造パターンを導き出したり、商品としての機能性を向上したりできます。
経費削減
IoTを導入することで経費削減もできます。これにより損益分岐点 (黒字化に必要な最低収益額) を引き下げられます。
IoTデータをもとに、製造計画にあわせて最適な手順・人員・人数を把握して実践することで、余分な経費を払わずに済み、作業効率も向上します。
人手不足の解消
IoTデータをプログラミングされた AI を導入し、作業を代行させることで人手不足を解消できます。定期的なメンテナンスは必要ですが、人間だけで行うよりも作業を効率的に進められることもあります。
常時モニタリングでトラブルに対応
IoTデータのなかには映像などで常時モニタリングできる機能もあります。工場の機械にトラブルはないか、作業者が安全な状況で仕事できているかなどを監視することで、納期に響くようなトラブルや事故を予防できます。
工場・製造業でIoTを取り入れるメリット
製造の現場にIoTを導入することで、効果が出るメリットは主に3つあります。
楽に現状把握ができる
工場に関するあらゆるデータを「見える化」できます。現状把握のために整理すべきデータを IoT システムひとつにまとめることができるので、余分な手間を極力省いた状態で 知りたい要素を把握できます。
さらにIoT機能で知ったデータを、今後の工場の運営方針に役立てられます。データから現状を分析することで、問題を解決するヒントを見つけられます。
省エネが可能
IoT化により、必要なときに必要な分だけのエネルギー使用を実現できます。
工場では機械をはじめ様々な部分でエネルギーが消費されています。大量の水が使われ水道代がかさんだり、工場を動かすための電気やガス代が高くついたりします。こうした必要経費を少しでも削減したいと望む事業者は多いです。工場から出る煙の量の多さで、周辺住民への影響を心配する人もいるでしょう。
IoT 導入により、作業に必要な最低エネルギー量を把握できます。エネルギーの消費量が多すぎる場合は、供給量を下げるなどの調整も可能です。以上の実践により、余分なエネルギーを抑え、従来より健全な環境で作業を進められます。
職場環境を改善し、生産効率を高められる
IoT化は作業効率だけでなく、職場環境の改善にもつながります。
モニタリング機能で作業員をチェックすることで、事故を未然に防ぐことができます。また、IoTデータをプログラミングされた AI の導入で作業効率が上がり、人手不足や作業員の疲弊を解決できます。
工場内の温度や、ゴミの散らばりなどをデータ化することで、作業員が健全に働けるように環境を改善するヒントも得られます。
工場×IoTの「見える化」事例
工場などの製造現場のIoT化の事例を3つ紹介します。
YKK AP株式会社
CMでもおなじみのYKK APでは2013年6月にIoTを導入し、工場内のデータを可視化しました。
同社がIoT化で注目したポイントは、空調設備のエネルギー節約です。窓を開けて吹き込む風を利用し、適切な空調設備の使い方を見極めたのです。
例えば夏の間は、気温の低い夜間・午前中は工場全体の窓を開放し、涼しい風で暑さをしのぎます。
モニタリングにより風の向きや強さ、気温・湿度などをリアルタイムでデータ化し、風だけで工場内を快適に過ごせるのか、空調が必要な時間はどれだけかを把握します。
空調設備を動かすべき時に入れば、各エリアの窓担当が窓を閉め、空調を操作します。
これにより、夏場の生産重量ごとに費やした空調エネルギーを約17%節約しました。
YAMAHA
YAMAHAでは、Motion Boardというツールで月間実績を1日ごとに細分化しました。
情報システム部門に頼らず、生産現場だけでIoTの力を借り、生産効率、不良品の発生率、非生産時間からなる生産関連ステータスをまとめ、ハイレベルな作業効率を実現させるための仕組みを作り上げました。
従来は生産に関するデータは手書きで、それをMicrosoft Excelに反映していましたが、それにより経営層への報告まで時間差が生じ、問題解決が遅れていました。しかしIoT化により、生産に関するデータをまとめる手間と時間を省き、年間2,000万円の経費削減に成功しました。
富士ゼロックスマニュファクチュアリング株式会社
iPadでの直接入力やBI (ビジネスインテリジェンス) を利用したリアルタイムモニタリングで、生産データをリアルタイムで記録できる体制を整えました。
ビジネスインテリジェンスとは、企業に関するデータを収集し、蓄積、分析、報告などのコントロールを行うことで、経営上の意思決定のヒントを与えるシステムです。
富士ゼロックスでは、日報をPCにデータ化して落とし込む手作業で生産データが記録されていましたが、IoT化によりそのような手間が省かれました。
作業者がiPadに直接入力したデータが日報になり、ボタンを押すだけで総合データに組み込まれます。それは工場内の大型モニターに出現し、作業員全員に「見える化」されました。
その結果、問題を解決するための対応協議もリアルタイム化し、素早い解決につなげられました。
まとめ
工場では多くの情報がデータとして把握できない、トラブルによる納期の遅れや事故、人手不足などで評判に影響が出るなどの問題がたびたび起きています。
しかしIoT化やAI導入などで、工場で起きていた問題の多くを解決することができます。データ化による作業効率の上昇、従業員にとっての労働環境を改善、安全の確保など、前向きな効果が望めます。
実際にYKK APや富士ゼロックスなど、IoT化で工場内の作業効率や環境を向上させた大手企業も存在します。工場の IoT 化は、導入した現場を変えるだけでなく、日本経済にも好影響を与える鍵といえるでしょう。